Для 33-летнего Игоря Перевезенцева ворота нескольких коттеджей нововоронежского «Поля чудес» в какой-то мере являются постоянно действующей экспозицией. Многие из них он делал своими руками – гнул металл, изготавливал декоративных зверей и птиц. Именно оттуда, из первой мастерской, расположенной в отцовском гараже, и начался его путь в бизнес, в котором он сегодня построил две успешные компании – ООО НПП «ИнтерПолярис» и ООО «Металлмаркет». О том, как обычный парень из города атомщиков, не имевший связей и высоких покровителей, стал одним из крупнейших работодателей Нововоронежа, – в материале РИА «Воронеж».
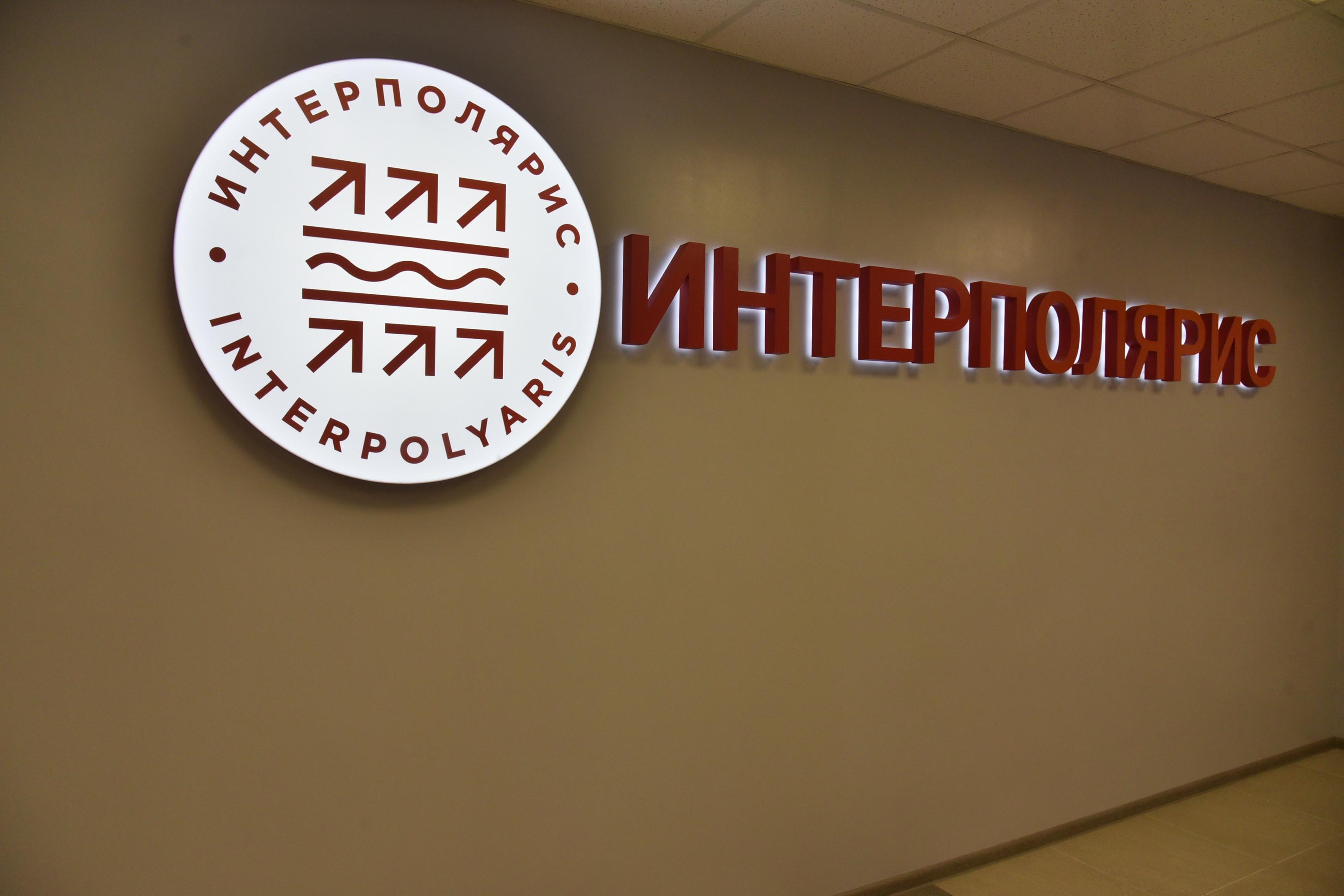
Как ковался бизнес
– Эти ворота я варил, кажется, в 2009 году, – вспоминает Игорь, показывая на затейливый узор какой-то ограды. – Тогда, конечно, в голове была уйма планов, но как их реализовать, не понимал вообще.
Закончив экстерном 10-й и 11-й классы в Нововоронеже, парень поступил в Нововоронежский политехнический колледж, где проучился до 2005 года. Затем уехал в Москву, чтобы продолжить обучение в финансовом университете по специальности «Коммерческий маркетинг». После учебы пытался устроиться на работу по специальности в столице, но тут был нужен опыт, а для наличия опыта необходимо было работать по специальности. В общем, замкнутый круг.
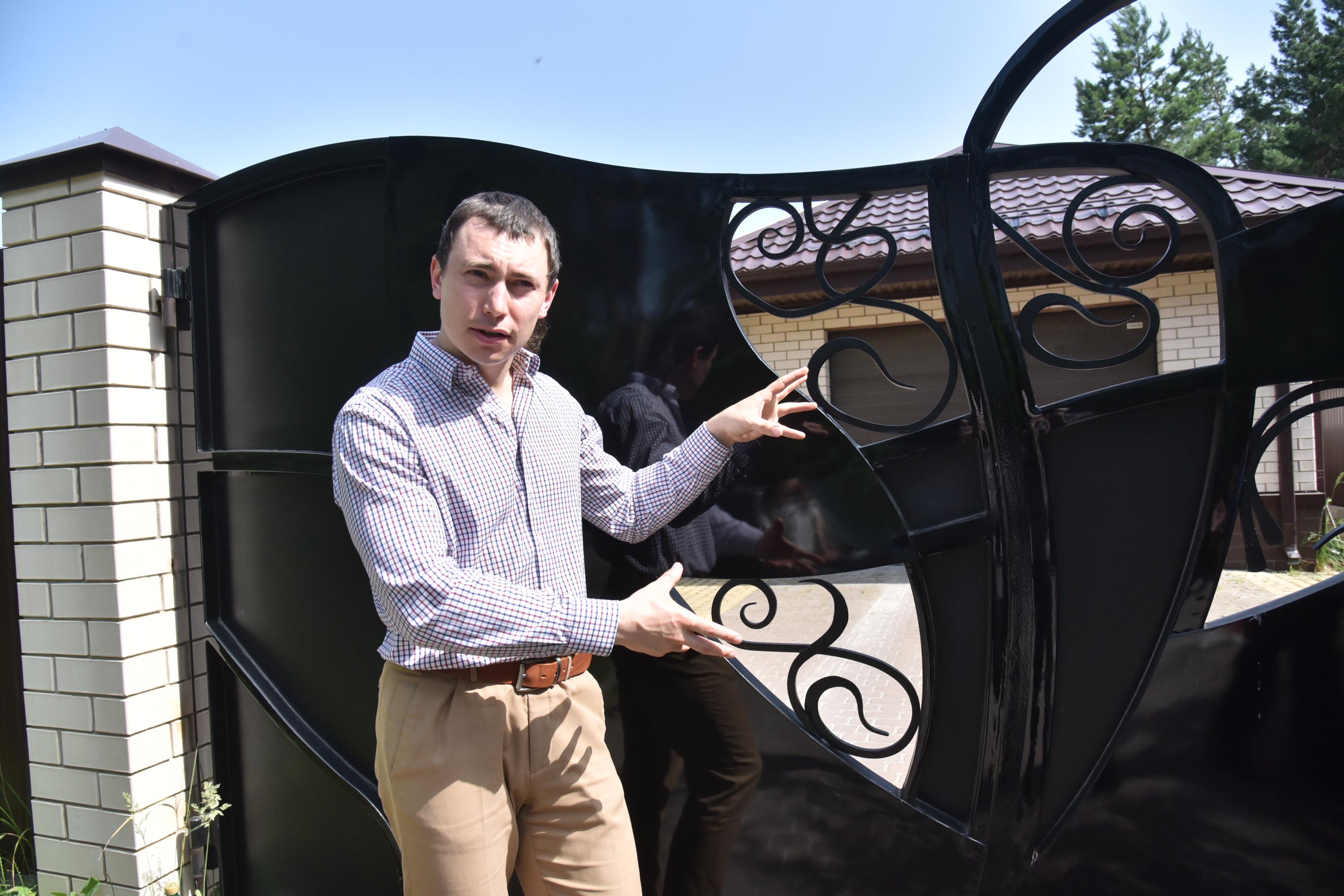
– Решил организовать свое дело, но опыта еще не было, как и знакомств в каких-то высоких сферах. Начинал в отцовском гараже. Набрал металлолом, привез кирпичи со свалки, посмотрел что-то в интернете – в общем, сделал свой первый кузнечный горн. Было это в 2008–2009 годах. Начал ковать ограды на кладбище, ворота, заборы. Первые года два я делал все сам, потом организовал ИП, подтянул людей, занялся организацией салона художественной ковки, арендовал помещение, выставил образцы своих изделий, нанял менеджера по продажам. Потом начал продавать металлопрокат. С утра до обеда принимал заказы на художественную ковку, потом шел выдавать металл, потом – на производство. Примерно через три-четыре года после начала у меня появилась хоть какая-то организация: менеджер, рабочие, кладовщик. Затем начал работать с муниципалитетами по всему ЦФО: изготавливали остановки, торговые павильоны, уличный спортинвентарь, мусорные баки, контейнерные площадки, дальше дошли до «умных» остановок. В это время, в 2015–2016 годах, у нас уже работали порядка 30−40 человек.
Дальше – больше. Игорь вспомнил свое студенческое увлечение, связанное с естественно-научными темами, и с товарищем организовал конструкторское бюро (КБ).
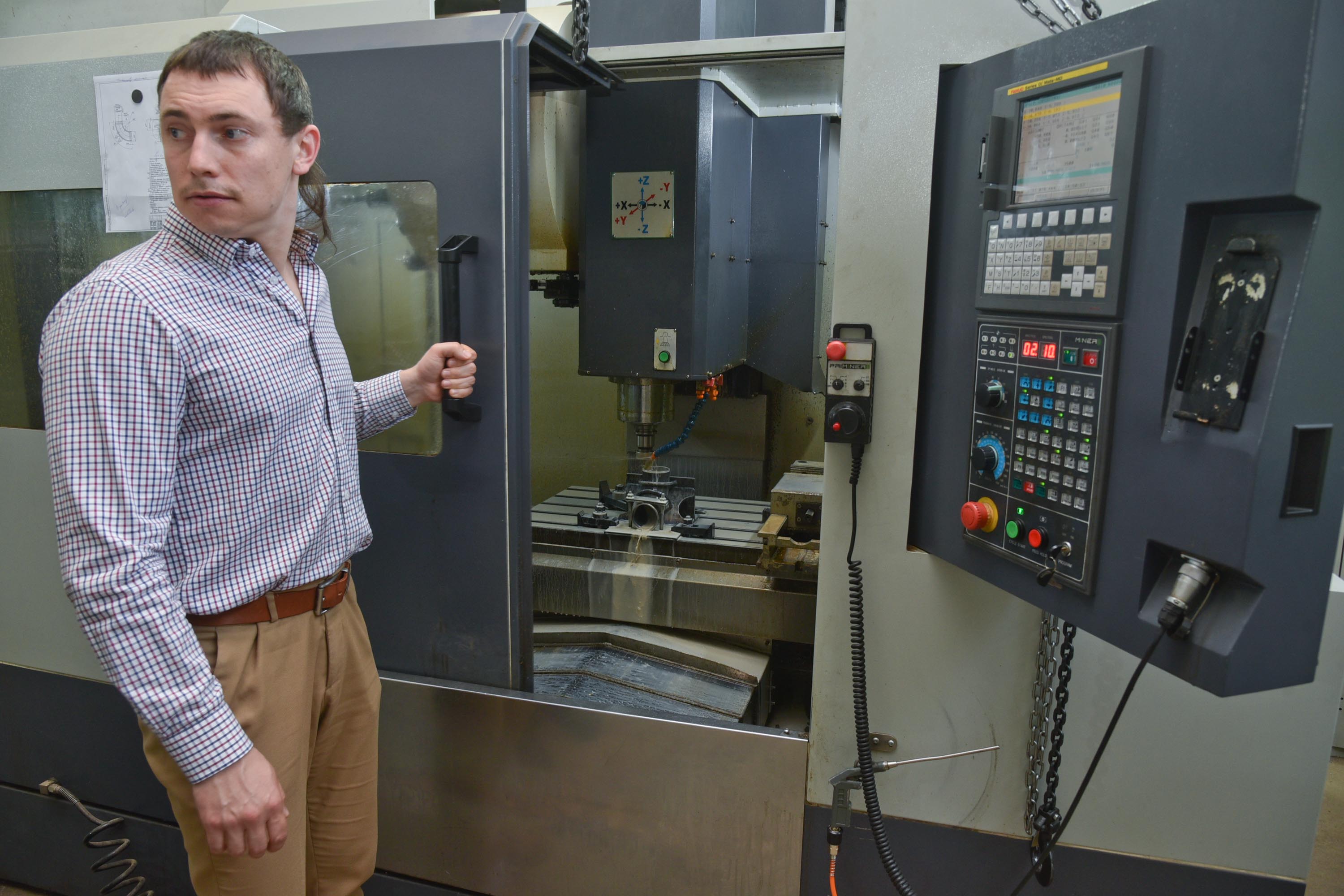
– В 2013 году появилась фирма «ИнтерПолярис», которая занималась инжиниринговым аутсорсингом – мы оказывали промышленным предприятиям услуги по разработке продукции. Предприятие, допустим, производит какую-то серийную продукцию, а ему нужно ее как-то усовершенствовать, изменить параметры изделия. Но у них нет своего КБ, они не имеют возможности разработать новую продукцию. Вот они и обращались к нам с тем, чтобы подготовили им эту разработку. Мы старались не задирать цены, так пошагово и входили в рынок. Потихоньку формировался наш инженерный корпус, сегодня у нас уже работают порядка 40 инженеров плюс наше подшефное студенческое КБ в Воронеже, – поясняет предприниматель.
Цена... в цене
Параллельно развивался и «Металлмаркет» с производственными компетенциями, а также «ИнтерПолярис» с компетенциями научных разработок. И в какой-то момент было принято решение объединить два производства и изготавливать своими руками то, что придумали свои же светлые головы. Это случилось примерно четыре года назад, тогда на производстве были простейшие станки для изготовления несложных изделий. Игорю стало понятно, в каком направлении двигаться дальше.
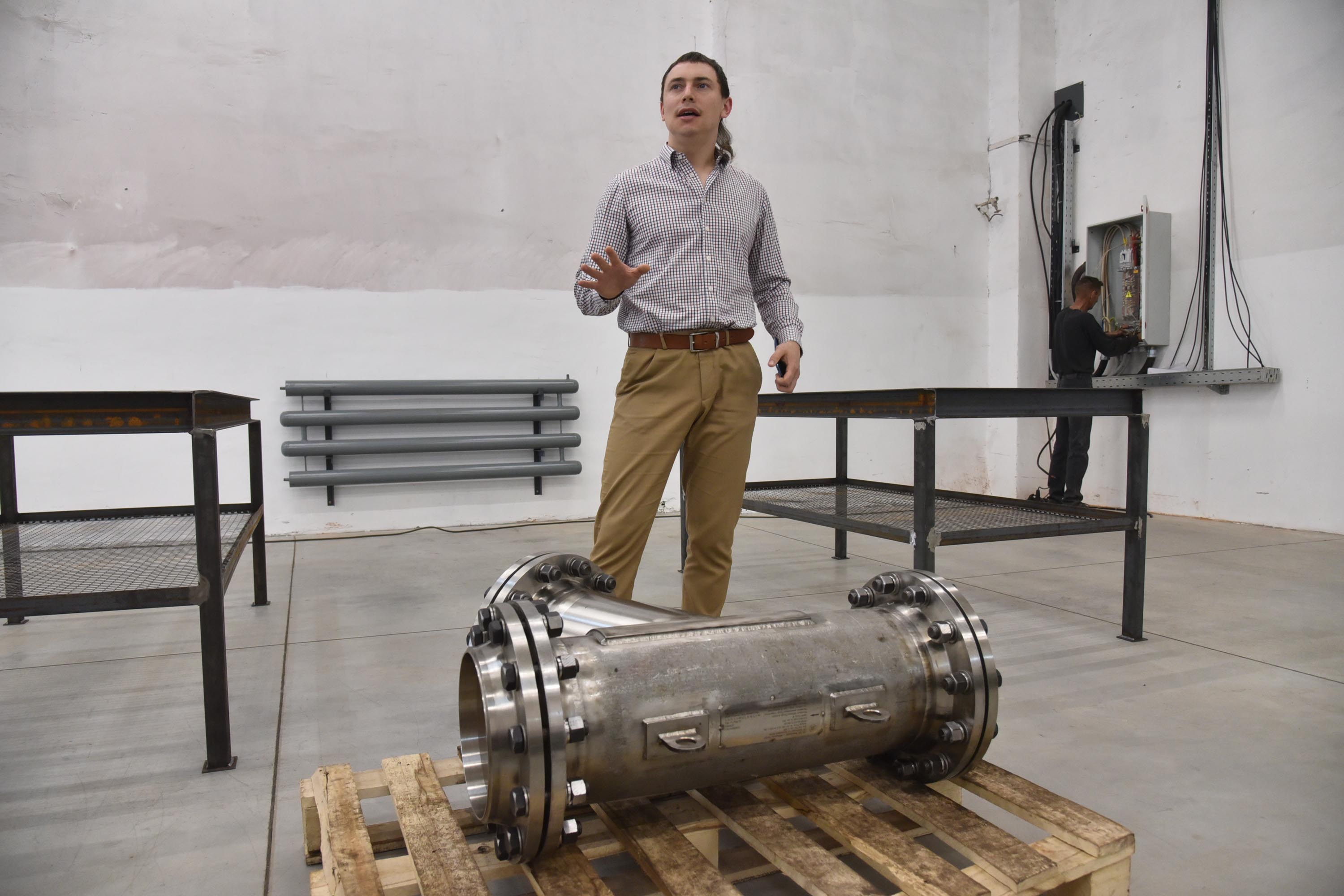
– Первый серьезный заказ мы выполнили для Нововоронежской АЭС. Во время проведения планово-предупредительных ремонтных работ у станции появилась потребность в стендах радиационного контроля. Как это бывает – выложили тендер, сроки были сжатые, но стоимость заказа обоснованная. Как сейчас помню, около 100 млн рублей. Ознакомились с условиями конкурса, собрались в цехе и начали обсуждать – «Сможем ли выполнить этот проект?» и «Что для этого нужно?». Главная загвоздка -оформление лицензии на конструирование и изготовление оборудования для блоков атомных электростанций. Это был первый шанс громко заявить о себе, и мы решили действовать. Собственно, заказ нам и достался, никто кроме «ИнтерПоляриса» в эти сроки сделать стенды не взялся.
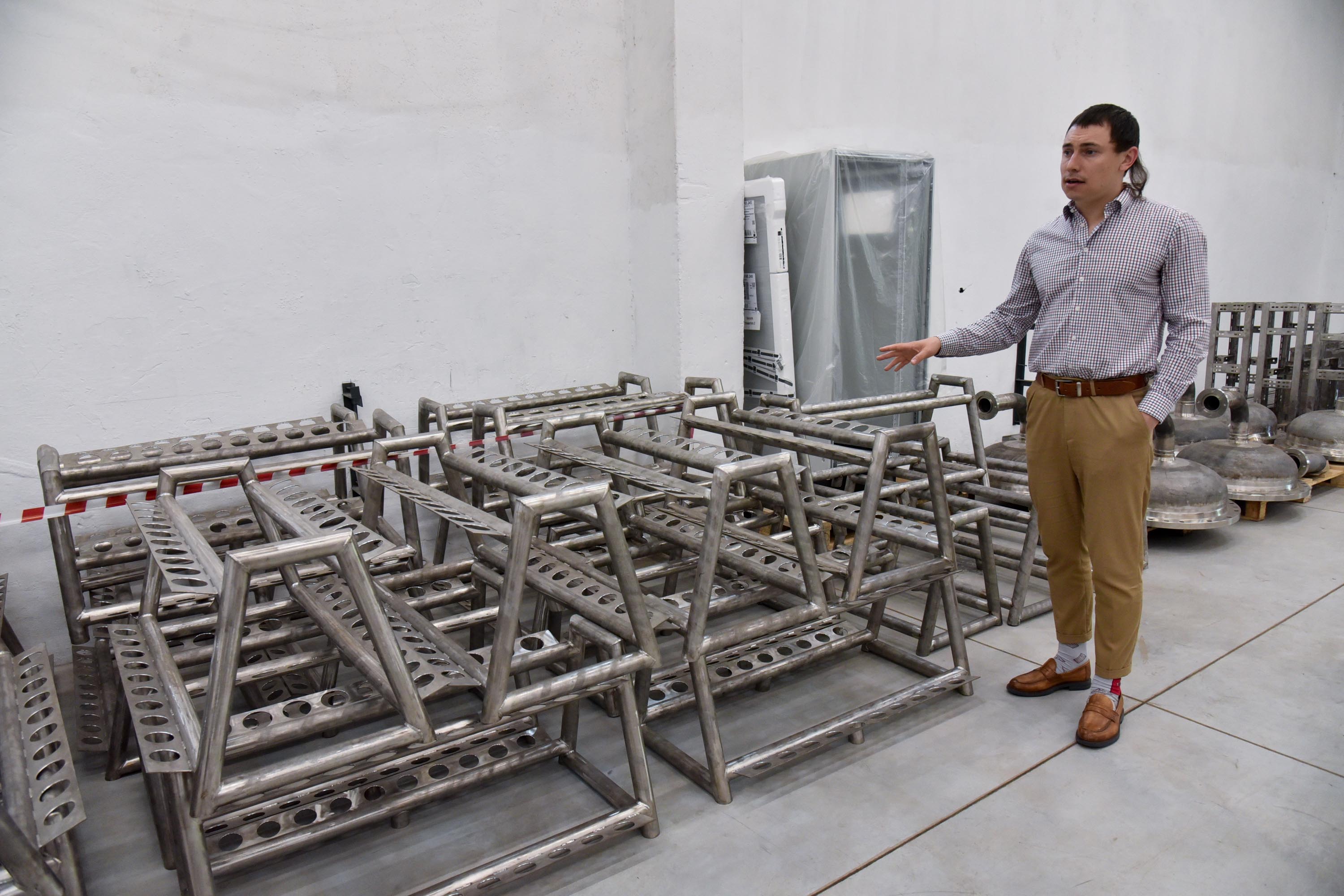
– Сейчас мы работаем по всему миру, делаем для атомных станций не только стенды, но и различное оборудование: фильтровальное, транспортное и транспортно-технологическое, контейнеры, гидравлические и пневматические системы, оборудование для СПГ (сжиженного природного газа). В арсенале шесть лицензий на разные виды работ в нашей отрасли. Сотрудничаем с Бангладеш, Китаем, Индией, Турцией, Венгрией, Арменией, а также и с технологическими лидерами Российской Федерации – «Роскосмосом», «Росатомом» и «Ростехом». Думаю, 60−70% общего объема нашего производства приходится именно на отрасль атомной энергетики, – объясняет Игорь Перевезенцев.
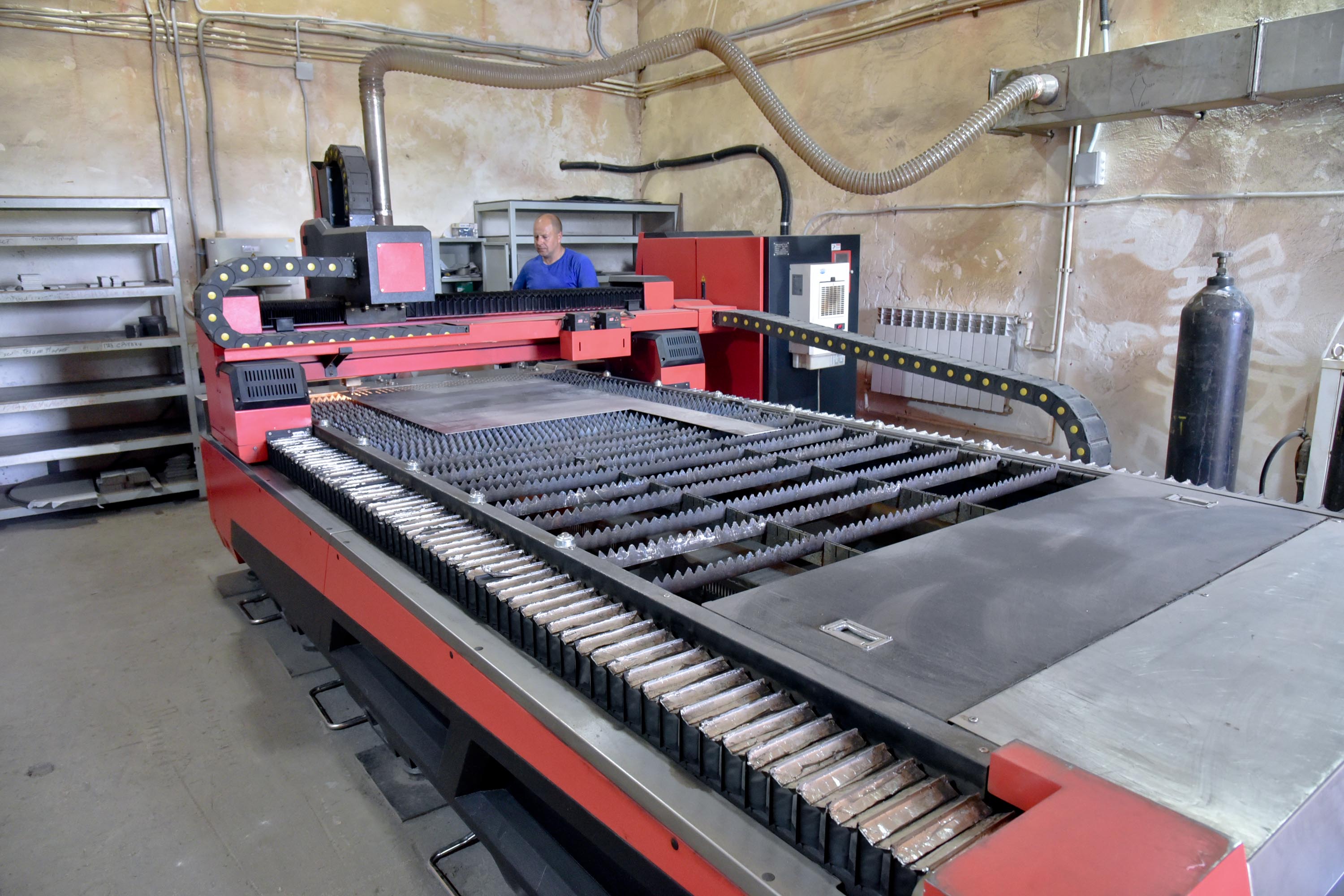
Качеству оборудования для объектов ядерной безопасности уделяется особое внимание и со стороны производителя, и со стороны заказчика.
– Группа компаний работает в таких сферах, где безопасность является приоритетом. В своей деятельности мы строго придерживаемся регламентированных норм и требований, предписанных государственным и отраслевым стандартами. На обеспечение качества того, что мы делаем, уходит примерно половина всех наших затрат, – отмечает руководитель. – Это и всевозможные аудиты от сертификационных и экспертных организаций, проверки от представителей АЭС, на которых будет использовано оборудование. Это разработка ряда документов по обеспечению качества изделий, которые необходимо согласовать с заказчиком, с генеральным заказчиком, с субподрядчиком и т. д. Перечисленные операции необходимо выполнить только для того, чтобы приступить к проекту. Представьте себе количество процедур в процессе производства или же при отгрузке!

А на вопрос корреспондента РИА «Воронеж», за счет чего удается держать относительно низкую цену на этом рынке, последовал ответ:
– «Росатом» сегодня сильно наращивает темпы строительства и ввода в эксплуатацию новых объектов – сейчас, по-моему, строится более 30 новых энергоблоков. И если компания большая, крупнее нас, то она менее разворотлива. У больших компаний – большие издержки, дольше сроки исполнения заказов. И это влияет на цену. У нас – минимальные издержки, эффективнее выстроены процессы внутри компании, поэтому мы выдерживаем оптимальные сроки исполнения заказа. Кроме того, стараемся не завышать цену.
Про импортозамещение
В основном предприятия Игоря Перевезенцева работают на отечественных комплектующих, некоторые изготавливаются в этих же цехах – и условная гайка, и болт, и клапан. Так проще, потому что в атомной отрасли особые требования по качеству и купить гайку, сертифицированную по всем требованиям безопасности, сложнее, чем наладить выпуск таких у себя.
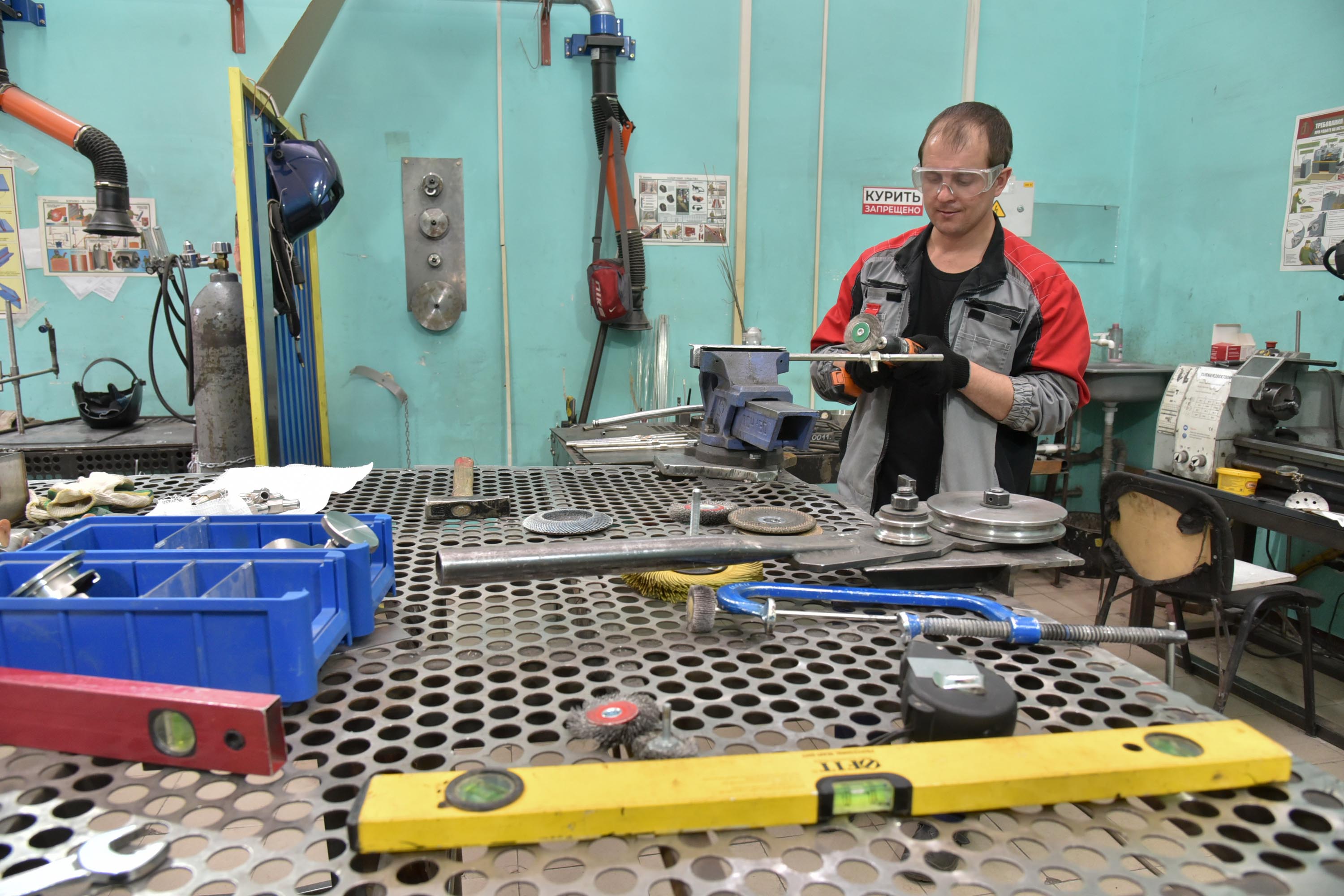
– А что касается импортных комплектующих, то там есть сложности, которые пока мы не можем преодолеть. Если какое-то сложное оборудование делают условно два производителя во всем мире, то ни одна страна даже за десять лет не сможет его быстро освоить. Мы, как и все, столкнулись с проблемой поиска отдельных видов комплектующих. На сегодняшний день часть наших проектов, связанная и с импортными деталями, временно зависла. Мы стараемся как-то выходить из положения предложением таких же насосов, например, китайского производства, пытаемся согласовать с заказчиком иные импортные комплектующие, не те, которые были согласованы раньше, а другие. Но в атомной отрасли эти процессы небыстрые, – отметил Игорь Перевезенцев.
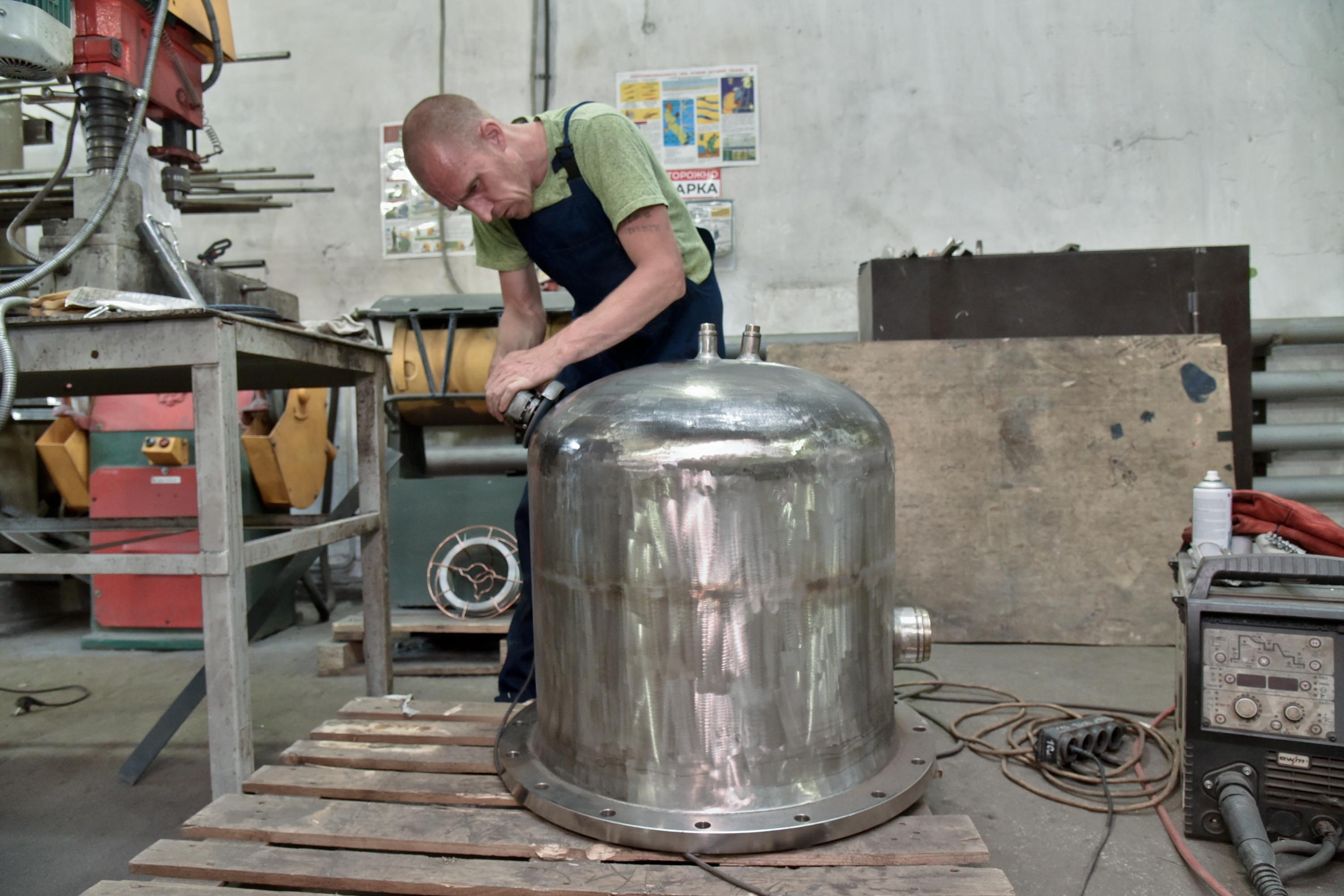
Но все-таки на предприятии нашли выход из положения.
– Мы предлагаем различные варианты, например, перейти на другое оборудование, рассматриваем тему с реимпортом, заменой техпроцесса в целом. Есть проекты, в которых удалось найти замены, есть те, в которых что-то произвели самостоятельно. Вышло, конечно, дороже. То есть по-разному решаем эти вопросы, – рассказывает Игорь.
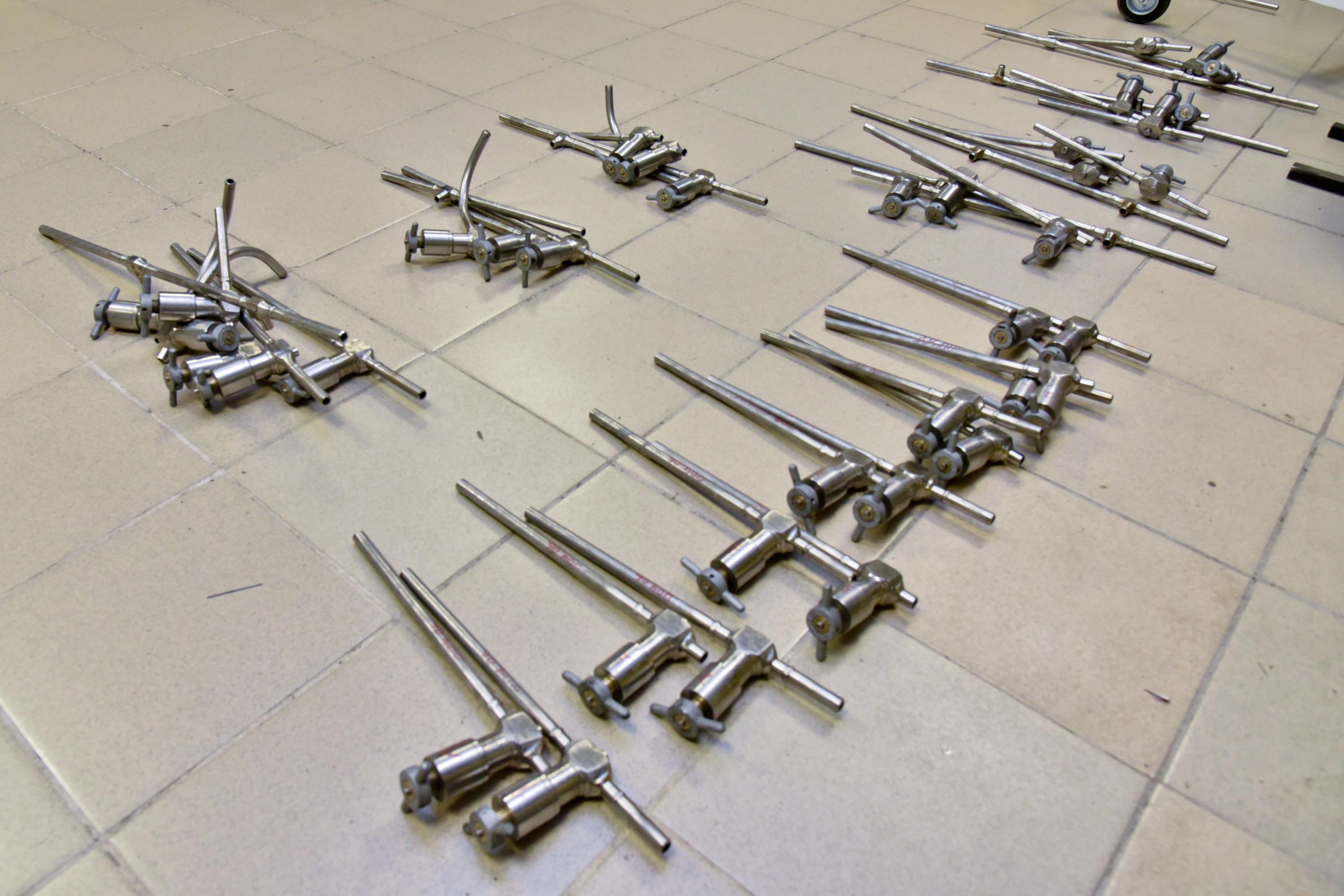
Меньшие по объему, но очень важные сферы работы предприятия – производство высокотехнологичного оборудования для отраслей двигателестроения и ракетостроения. Здесь речь идет, например, о метрологическом оборудовании устройства контроля потока воздуха на входе и выходе двигателя. В компании разработана собственная методика и технология его создания. Также для этой отрасли производятся стенды для контроля давления в нефтяной и газовой промышленности либо расходные стенды, обеспечивающие подачу необходимого количества компонентов в тех или иных технологических операциях.
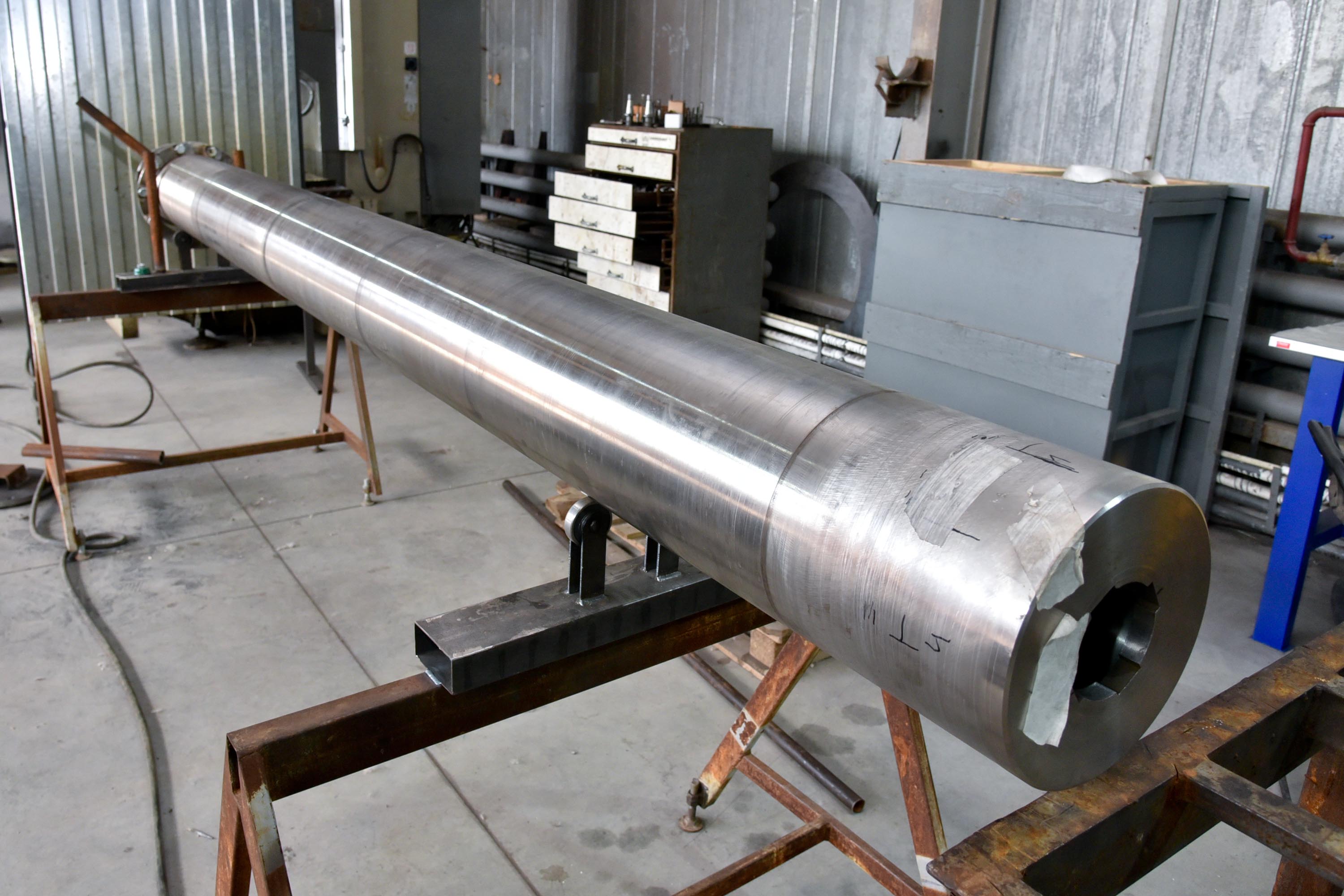
– В рамках того, что некоторые импортные комплектующие мы не можем купить, мы их делаем сами и что-то планируем продавать на внутреннем рынке. Речь идет либо о несложных изделиях типа устройства расхода газа (раньше покупались в Германии), либо о некоторых деталях трубопроводов, клапанах, работающих в криогенной среде при низких температурах, либо о клапанах запорно-регулирующей арматуры, – отметил руководитель.
Руки – на вес золота
В 2020 году предприятие выкупило территорию бывшего завода «Алиот» для того, чтобы развивать свое производство, но столкнулись с кадровой проблемой – некого поставить на станки, нет инженеров, технологов. Это была проблема № 1. Сейчас в компании готовы расширяться и принять на работу технических специалистов.
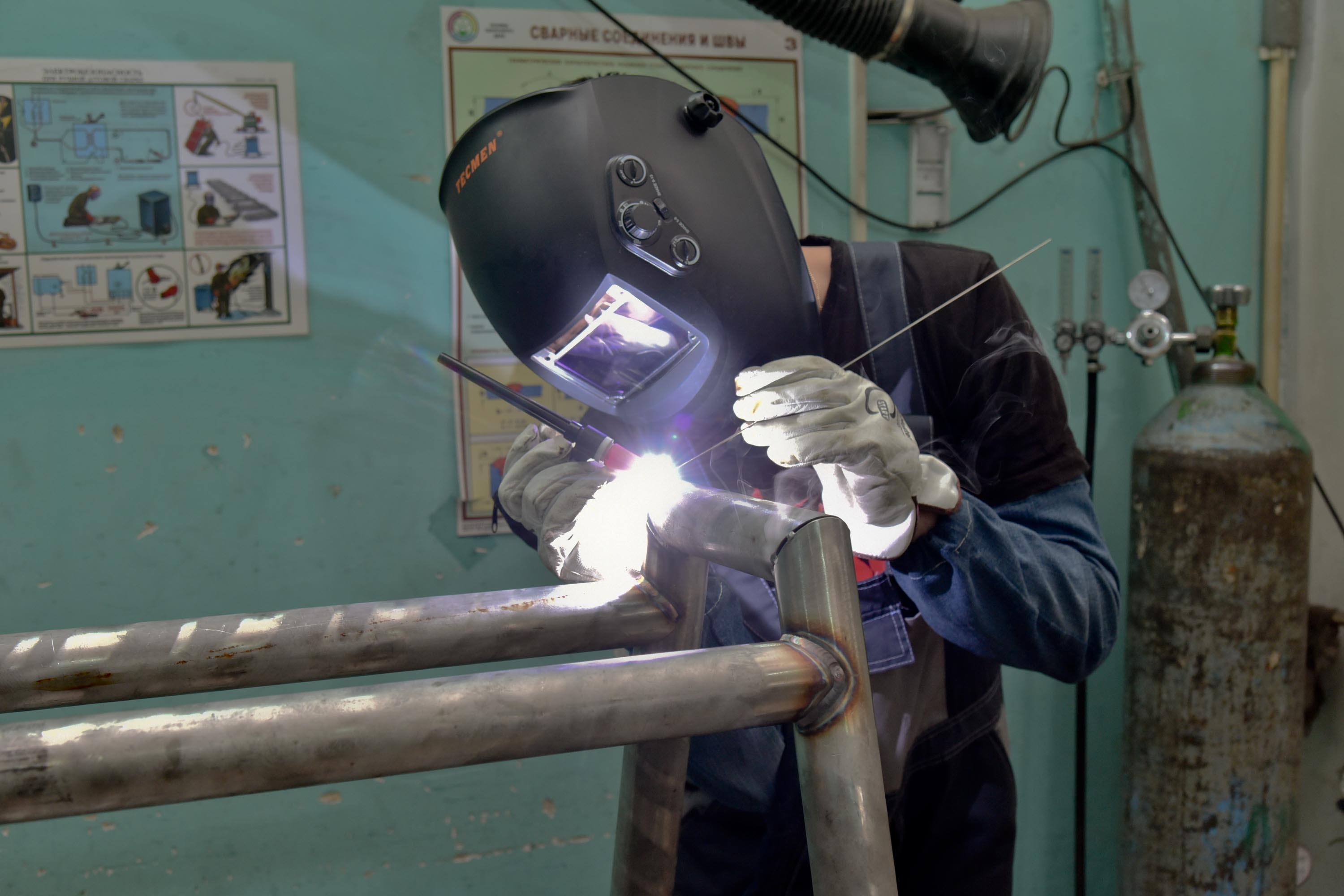
– Сегодня востребованы все специальности. С импортозамещением сейчас потребность в рабочих руках и инженерных головах возросла, мы готовы принять на работу примерно 150 человек (сейчас всего у нас работают столько же), владеющих различными специальностями. Нам требуется, во-первых, производственный персонал (рабочие, слесари, сварщики, токари, фрезеровщики, операторы станков ЧПУ, наладчики, программисты, начальники цехов, мастера, бригадиры), во-вторых, ИТР-персонал (технологи, конструкторы, расчетчики, инженеры разных специальностей) и, в-третьих, люди в административно-бытовой блок.
Вперед – к «оборонке»
По словам собеседника, предприятия могут сегодня наращивать объемы производства в разы, брать и выполнять миллиардные контракты.
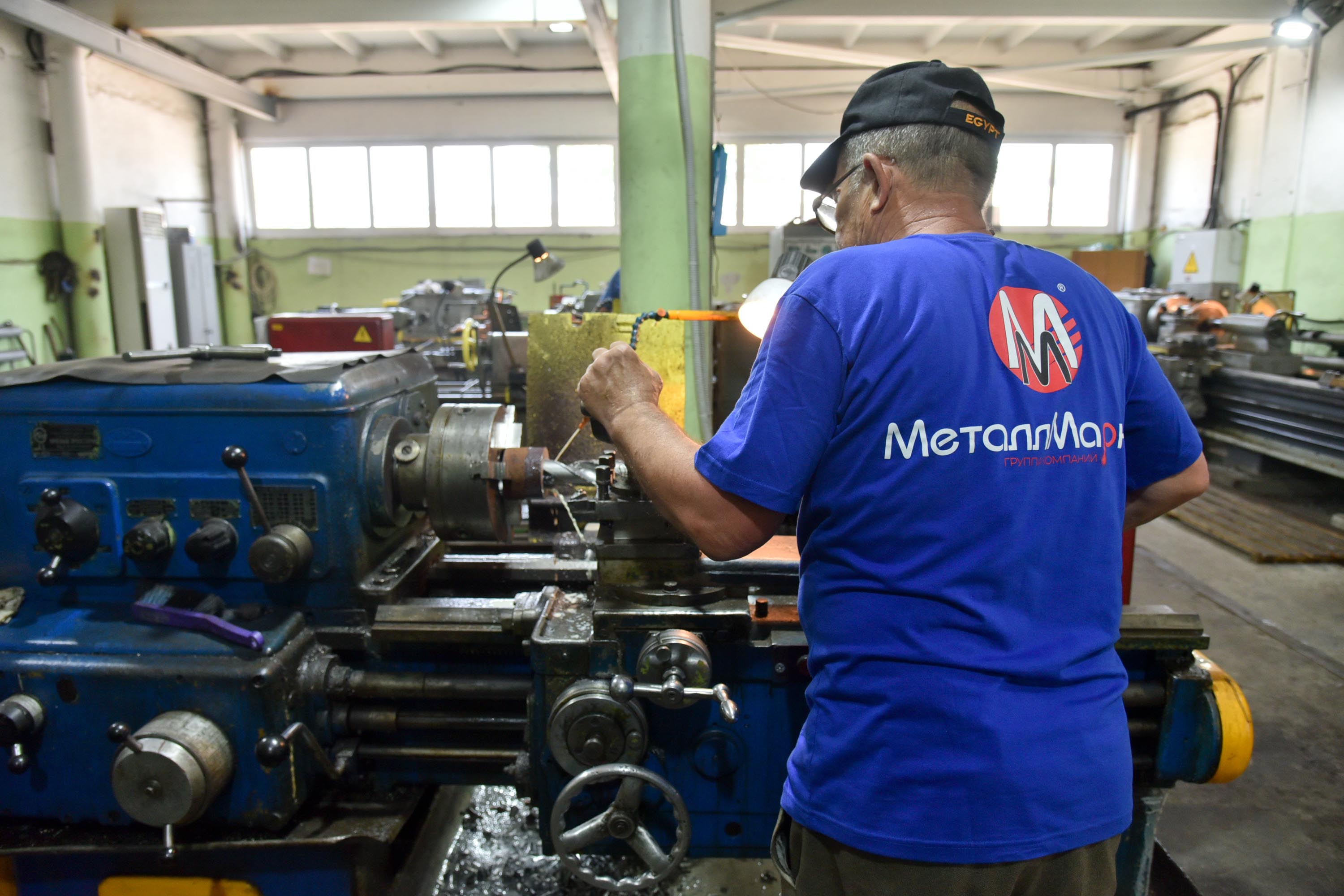
– Импортозамещение стало неким пинком, давшим движение в сторону расширения объемов производства. Наша ближайшая цель – зайти со своими разработками и изделиями в нефтегазовую отрасль, поработать в «оборонке», – делится Игорь Перевезенцев. – Теперь работодателям нужны квалифицированные кадры. Мы, например, в отдельных случаях готовы обучать наиболее ценных специалистов, платить людям стипендию на весь этот период. Кстати, в Воронеже у нас есть свое студенческое конструкторское бюро, куда мы набираем третьекурсников воронежского политеха и даем реальные задачи, выполнение которых оплачиваем. Некоторые ребята потом оттуда приходят к нам на работу.
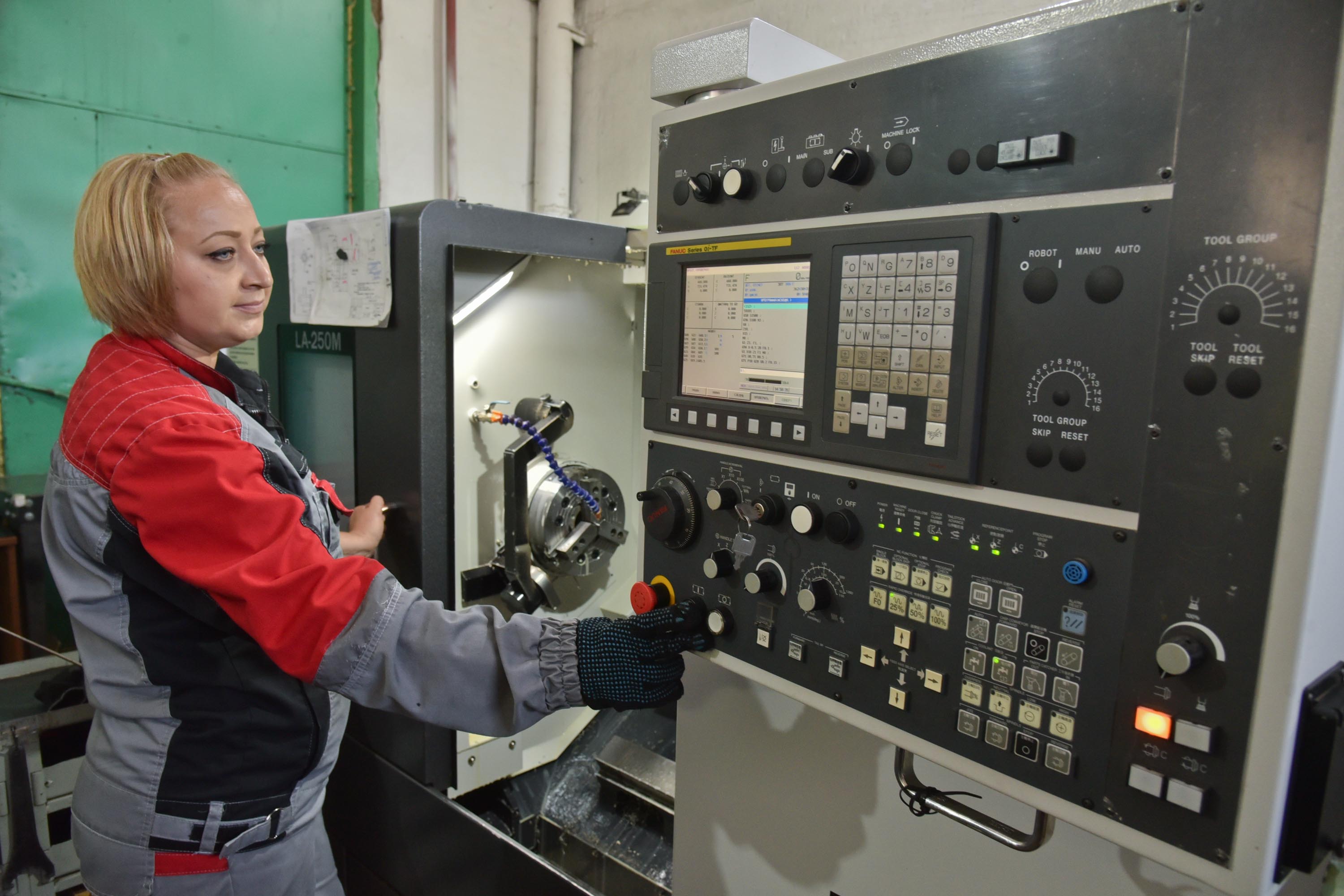
Те, кто уже стал частью коллектива предприятия «ИнтерПолярис», поделились с журналистом РИА «Воронеж» своим мнением о работе в компании.
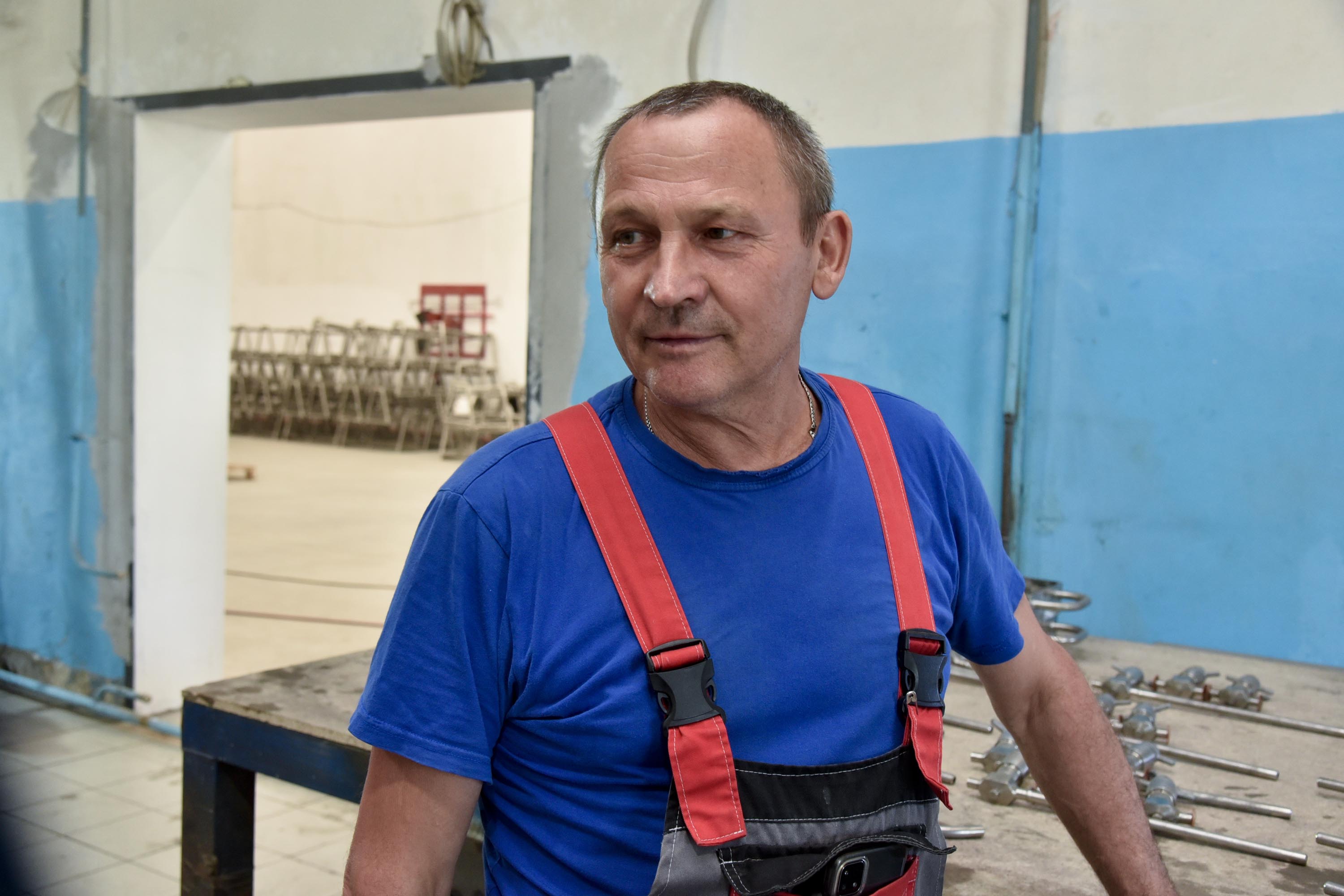
– Я электрослесарь 6-го разряда, – рассказал Александр Кучин, – работаю здесь два года, видно, что производство постоянно находится в развитии, работы становится все больше и больше, и это хорошо!
Андрей Ливерко – оператор станка лазерной резки металла – профессию освоил в этих стенах, а до того долгие годы отработал слесарем в местном автопредприятии.

- Новое дело мне показалось интересным, и хотя уже в зрелом возрасте пришлось поменять профессию, об этом ничуть не жалею, – отметил Андрей.
А дефектоскопист Алексей Щеблыкин – важная инстанция, проверяющая качество сварных швов всех деталей для будущих блоков АЭС, которые находятся в разных концах мира.
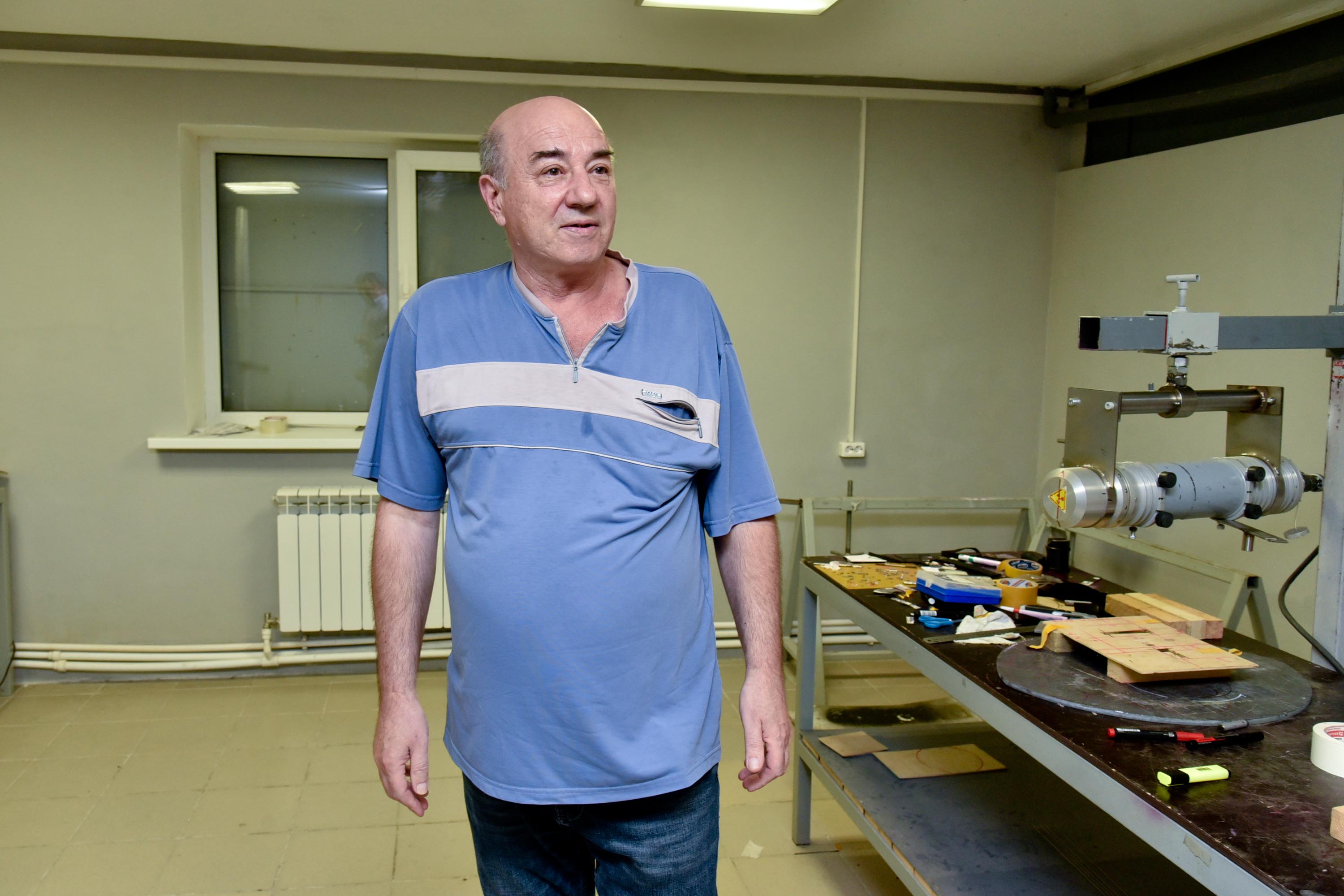
– Если вижу какой недочет, отправляю изделие обратно в цех, – отметил он, – но такое в принципе случается крайне редко. Здесь люди дорожат своей работой и стараются делать ее хорошо.
ООО "ИнтерПолярис"
На правах рекламы